The paradox of fusion energy is that it is always 40 years away, and has been for some 60 years. So scoff the fusion skeptics. And if you look at the projected timelines of the large intergovernmental fusion projects like ITER in France and NIF in California, you could easily join the ranks of those not holding their breath. But as I’ve written here before, there are a number of smaller and privately-backed fusion initiatives that could solve the fusion riddle long before the ITERs or NIFs do.
One of those companies is Helion Energy, a Redmond, Washington-based company that claims it will build a 50-MWe pilot of its “Fusion Engine” by 2019 after which licensees will begin building commercial models by 2022. That’s hardly the 40-year odyssey we’ve long heard about. Helion will obviously have to overcome many challenges in order to take the express lane to fusion land.
I won’t write about all of them in this post. But what strikes me as particularly relevant to Weinberg readers is how Helion (and the fusion community in general) is facing materials challenges and decisions that are similar to those confronting developers of alternative fission technologies like fast reactors and molten salt reactors (MSRs).
For example, Helion is contemplating the use of FLiBe – the molten salt that’s part of MSR designs – as a coolant and an electrical insulator. It’s also examining the abilities of different metals to withstand ferocious neutron bombardment – just the sort of thing that many fission researchers are also investigating as they try to move away from conventional fission reactors and to higher temperatures and other alternatives.
FUSION’S PROMISE
Before I dive into Helion, and in case anyone needs a refresher, Fusion joins atoms together rather than splits them apart as fission does. Many experts regard it as the Holy Grail of energy sources, noting among reasons that fusion does not leave long-lived high-level waste; that it requires comparatively little fuel and its fuel is to a large extent easy to obtain and plentiful; and that it cannot meltdown (even if it does require temperatures of over 100 million degrees C) and leak harmful radioactivity. (It also creates helium, a substance with many uses but one that is in increasingly short supply).
“Fusion has the potential to provide nearly limitless, clean energy for both baseload and on-demand power,” notes David Kirtley, Helion’s interim CEO, who I spoke with via Skype recently. “Fusion fuels are inexpensive, sustainable and can be supplied with minimal environmental footprint.
Don’t try this at home. Helion has built and tested an experimental version of the engine without the coolant and heat exchanger.
Helion’s small “Fusion Engine” uses principles of magnetism to generate heat that induces isotopes of hydrogen to fuse. But it bears little visual resemblance to the giant 20-story “tokamak” that ITER is building in Cadarahce, France using different techniques of magnetism. The Fusion Engine is a 28-meter long, 3-meter high bow tie-shaped device that at both ends converts gases of deuterium and tritium (isotopes of hydrogen) into plasmoids – plasma contained by a magnetic field through a process called FRC (field-reversed configuration).
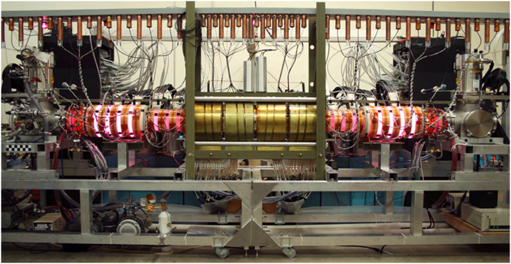
It magnetically accelerates the plasmoids down long tapered tubes until they collide and compress in a central chamber wrapped by a magnetic coil that induces them to combine into helium atoms. The process also releases neutrons. The Fusion Engine provides energy in two ways. Like in a fission reactor, the energy of the scattered neutrons gives off heat that ultimately drives a turbine. Helion is also developing a technique that directly converts energy to electricity. The direct conversion will provide about 70 percent of the outgoing electricity according to Kirtley.
IN AND OUT
The overarching problem that Helion, ITER, NIF, and others are working to solve is that the amount of energy it takes to coax sustainable fusion reactions is greater than what can be harnessed from the reactions. When you consider that temperatures inside many fusion designs hit 150 million degrees C, albeit briefly, then you can start to appreciate the amount of energy required to get things cooking.
In Helion’s case, it is powering capacitors that convert the deuterium and tritium gas into plasmoids. It is also powering electromagnets that surround the narrowing cylinders through which the plasmoids shoot. The pulsing magnets induce the plasmoid to accelerate. A fusion chamber also requires durable materials – doubly so since neutrons bombard the inside walls, severely testing their durability (except for in a process called “aneutronic fusion,” but more on that another time). Therein lies one of the main crossover points between fission and fusion development.
Both are looking for materials that can handle high energy neutron bombardment and high temperatures. Although fusion has a kinder brand image than fission, the fact is that it sets neutrons racing about just as fission does (again, aneutronic fusion does not do this). For Helion, this means finding the right material to line the inside of the compression chamber where the plasmoids collide and release neutrons.“This wall is exposed to high levels of radiation and high thermal load,” notes Kirtley. Helion is considering alloys including tungsten, beryllia and molybdenum.
These materials will be familiar to engineers and scientists working on high temperature fission reactors. As Kirtley notes, “the tungsten alloy claddings in high-temperature reactors absolutely share material crossover.” Helion’s collaborators on so-called “first wall” development include the U.S. Department of Defense and the University of Washington, he says.
A man of two fusions. Helion co-founder John Slough and his company MSNW are designing a separate fusion reactor, called the Fusion Driven Rocket, meant for spacecraft propulsion.
As important as durability is, Helion has another ace up its sleeve. It has devised a technique that allows for “rapid replacement” of the wall, a breakthrough that Kirtley describes as “one of the key advantages” of the Fusion Engine. “We believe it is key to the engineering design of an economically feasible fusion energy system,” he says. In Helion’s Fusion Engine, a coolant material will form a blanket that absorbs the neutrons and their heat after the neutrons escape through the wall.
As is the case with some fission research companies, Helion is not yet sure what coolant it will use, although its preference is FLiBe – a molten salt of lithium fluoride and beryllium fluoride. The MSR reactor community will recognize FLiBe as one of the fluids that can serve as both a coolant blanket and a fuel carrier in an MSR. It is the substance that lends its name to Flibe Energy, the Hunstville, Ala. company that is developing a two-fluid FLiBe-based MSR. Helion is also considering using lithium as the blanket coolant.
Lithium is a common choice in fusion designs because it reacts with the neutrons to make tritium. Of the two hydrogen isotopes commonly used in fusion – deuterium and tritium – tritium is the more difficult to obtain (deuterium is found commonly in seawater), so a process that replenishes tritium via interaction with lithium is a popular design among fusion engineers.
Kirtley claims that Helion’s fusion process requires less tritium than do other fusion technologies and that the Fusion Engine makes some of its required tritium by fusing deuterium atoms in the collision.
“Our reactor design removes the majority of the complex tritium producing blanket,” says Kirtley. Thus Helion has less need to breed tritium from lithium and it is therefore looking seriously at FLiBe, which is a more effective, less expensive and less problematic coolant than lithium, he notes.
FLiBe’S FUSION HISTORY
The idea of using FLiBe as a fusion coolant is not new. The U.S. Department of Energy’s Idaho National Laboratory has investigated it in partnership with Lockheed Martin, the aerospace stalwart that is also developing a fusion reactor. Likewise, Ralph Moir, the physicist known for his interest in hybrid fission/fusion reactors, published a paper on a fusion FLiBe coolant over 20 years ago at Lawrence Livermore National Laboratory in which he notes that FLiBe avoids the fire hazards of lithium as a fusion coolant.
MIT and Argonne National Laboratory published separate papers on FLiBe and lithium’s usefulness in fusion reactors in the 1970s.FLiBe might serve a second purpose on Helion’s Fusion Engine as well. Kirtley says the company wants to use it to provide electrical insulation to the electromagnets. By using FLiBe for that function as well as for the coolant blanket, Helion would simplify its materials needs and lower its costs, he notes.
Helion’s design comes from company co-founder John Slough, who is also a research associate professor at the University of Washington and who runs Redmond-based space propulsion firm MSNW LLC. Slough is a fusion enthusiast, to say the least. He is designing a separate fusion reactor intended as a propulsion device that in principle could send manned spacecraft to Mars in 30 days.
That project known as the Fusion Driven Rocket, has funding from the U.S. National Aeronautics and Space Administration. The more earthly Fusion Engine has received about $7 million in funds from DOE, the Department of Defense and NASA. The company hopes to raise another $2 million by next year, $35 million in 2015-17, and $200 million for its pilot plant stage.
It will compete for development funds with other fusion initiatives, such as those at General Fusion, Lockheed Martin and the “aneutronic fusion” projects at Lawrenceville Plasma Physics and Tri-Alpha Energy. It will also compete against fission development. But given some of the material similarities with fission, it might also find itself in collaboration with some of those efforts.